Related Projects
OPTIMAI is part of the 4ZDM cluster, the European initiative around the Factories of the Future Zero Defect Manufacturing priority which aims to promote the adoption of zero-defect production and quality control systems by industry.
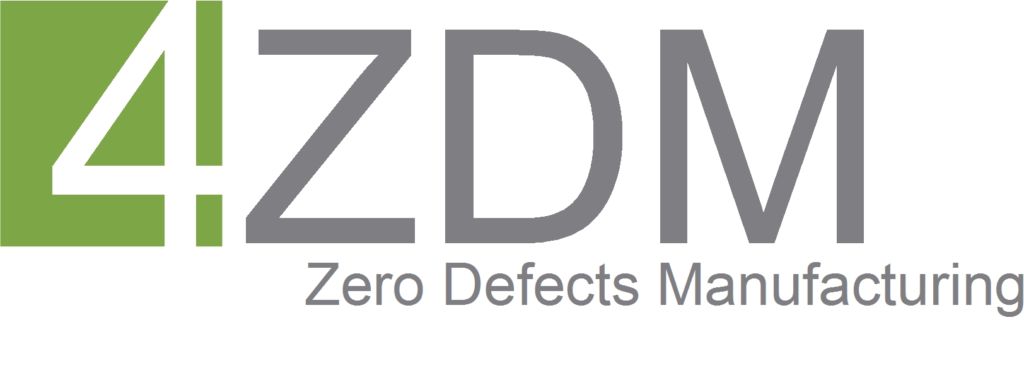
OPTIMAI’s sister projects funded under DT-FoF-11-2020/DT-FoF-10-2020 are InterQ, DAT4.ZERO, I4Q and PeneloPe.
Visit our joint website to find out more about the cluster: https://zdmanufuture.org/
Cluster Policy Brief
Additional related zero defect manufacturing / zero waste projects
Wind energy is becoming an increasingly mainstream part of the electricity mix, and they are an essential part to meet the Green Deal targets. Despite this, the technologies used to manufacture turbine blades have not changed significantly since the 1970s, including processes that are prone to defects and result in high rates of re-work, scrap, and repair.
In order to meet the worldwide demand for sustainable green energy, the wind industry needs to transform itself to be more resource-efficient and enable zero-defect and zero-waste manufacturing. The industry needs game-changing, innovative, disruptive, and ambitious ideas to produce new manufacturing methods.
TURBO, a project funded by the European Union’s Horizon Europe research and innovation programme, aims to contribute to these changes in the industry by combining several new developments from different disciplines and reduce defect formation and improve composite production on site. The researchers will experiment with cutting-edge non-destructive testing methods to monitor composite production on site.
The core of such procedure will be the development of machine learning-based algorithms for in-line process control during turbine blade production, which will help minimize deficiencies and waste, and optimize operational efficiency.
Among the developments that TURBO will bring to Industry 4.0 to transform wind industry, there is the enablement of data-driven manufacturing decisions to reduce defect formation and improved defect assessment; this will drive the scrap rate down as well as optimizing the manufacturing processes and decrease production waste.
More information can be found at: https://turboproject.eu/
This project is funded by the European Union under Grant Agreement No. 101058054
FLASH-COMP is a new Horizon Europe project that started in October 2022. The aim of the project is to bring novel digital technologies to the liquid resin infusion process (LRI), one of the most widely used manufacturing processes using composite materials. By bringing advanced automated controls and in-line defect monitoring and detection to the LRI process, FLASH-COMP will allow industry to cut material waste significantly, while also improving efficiencies in the process and the quality of products produced.
The project, which is coordinated by Lortek in Spain, is developing a fast and reliable (FLASH) human-oriented quality control solution that will identify defects in real time during the LRI process and, also in real time, determine any corrective actions needed that can be implemented in-situ. This will help eliminate waste from LRI processing, while at the same time eliminate defects in finished products produced using the LRI manufacturing process, so significantly reducing the generation of polymer composite waste.
Traditional LRI process
In LRI processes, after the product design phase, a multi-layer fibre preform is placed on a mould and infused by liquid resin. Once the resin is cured, a finished part can be extracted.
After trimming and finishing, defect identification is mainly based on visual inspection and other non-destructive testing (NDT) methods during the quality control phase at the end of the process and takes place off-line to locate, identify, and measure internal flaws like voids, delamination or spots in the manufactured parts.
Despite the high value of the parts produced using this process, both material processing and quality control are still largely done manually, with the quality of the final product being almost totally determined by an experienced operator. In most cases several reworking actions are needed during the process as well as repairs needed to the final product. In some cases, repair is not possible and the whole part is discarded. This happens in around 3% of cases.
Both these activities are usually complex and account for around 30 per cent of the total production time, which makes the whole process highly inefficient.
To overcome the lack of automated in-line control and to guarantee that the defects that do arise during the process are kept to a minimum and do not make their way into the final product, LRI manufacturing processes often use more materials than necessary. This is particularly the case with the quantity of resin used in the infusion process, resulting in an excessive amount of raw material used and waste generated at the finishing stage, when parts are trimmed and polished for example.
The FLASH-COMP approach
FLASH-COMP will employ novel, fast and accurate Inspection and Monitoring techniques (FLASH-IM) within the most critical manufacturing stages of LRI, pre-forming and infusion, to retrieve key process parameters. This data will feed an AI-based Defect Severity Estimation Tool (FLASH-DSET), capable of estimating the generation of defects and, consequently, determine if and what kind of corrective actions should be taken at the pre-forming and resin infusion stage of operations. Instructions will be linked to a real-time feedforward and feedback (FF/FB) control strategy Decision Support System (FLASH-DSS) which will allow workers to take instant and precise corrective actions paving the way towards ‘first-time-right’ manufacturing with zero-defects and zero-waste.
FLASH-COMP impact on LRI processes
FLASH-COMP technology will reduce the amount of liquid resin used in the infusion process as well as reducing the amount of trimming required at the finishing stage. Meanwhile, with corrective actions taking place in line during production, the process of detecting defects and then repairing or discarding them will be removed from the quality control phase and the final product will be right first time.
It is estimated that a reduction of waste of more than 30 per cent can be achieved in this sector. Waste will be reduced in cured composite off-cuts, resin residue and part rejections. For example, for a typical 2.0 MW turbine blade, which is 40 metres long with a fibre content of 53 per cent and epoxy resin, the environmental benefit will be quantifiable by a reduction from 0.55 to 2.8 kg CO2eq. per kilogram of composite for glass fibre and from 1.06 to 6.9 kg CO2eq. per kilogram of composite for carbon fibre.
Project image
The Azimut-Grande Trideck, a yacht built by Flash-Comp partner Azimut Yachts, an Italian yacht-manufacturing company based in Viareggio, Italy. The company uses LRI processes to build structures like its hulls. A complete FLASH-COMP solution, adapted to large scale production parts, will be installed and demonstrated as part of the project, integrating multi-spectral 2D cameras and 3D laser profilers for inspection of the preforming and layup stages, as well as FLASH-LiDAR and Pyzoflex® for the monitoring and control of the infusion process and resin cure.
The human aspect of FLASH-COMP
One clear message from the FLASH-COMP project is that the solutions are not designed to replace people – they are designed to help people do their jobs more effectively.
FLASH-COMP is creating a decision support tool that will help workers to control the manufacturing process by either intervening directly or providing suggestions on how to proceed to guarantee the correct progress of the process. It will therefore be essential to put proper consideration into how this interaction between the decision support tool and the person involved works, to ensure that the FLASH-COMP solution is both accepted and valued by those who use it.
FLASH-COMP will integrate the needs and requirements of the users in the technical development of the FLASH-COMP solution, and use their suggestions about how to make the solutions more user-friendly and useful. It will also look to understand the impact of the new solution on the current work environment, identifying learning objectives to help current and future workers cope with the technological, process and cultural change that may come with the new solution.
Knowledge and methodologies from social sciences and humanities (SSH) will play a key role in this aspect of the FLASH-COMP project, with the aim of involving the end-users and workers from the beginning to shape the solution and to properly consider the learning competencies required to assure an effective integration of the FLASH-COMP solution.
Several interviews with end users will take place at the beginning of the project, as well as observations of the different tasks they perform daily. Through an iterative process, the user’s perception of the technologies will be assessed and considered as the development of the solution progresses. This will be done through focus groups that include participants from a wide range of staff positions, from plant operators to management.
More information can be found at: https://flashcomp.eu.com/
This project is funded by the European Union under grant agreement 101058458
Manufactured metal products are used daily by most of the people on the planet; manufactured goods are a significant part of EU’s economy, and the market is expected to grow in the coming years.
The manufacturing process though is energy-intensive, requires substantial amounts of natural and financial resources; at the same time, a significant effort is needed to rework or recycle defective components and engines. In addition, European current way of life requires a competitive manufacturing sector to compensate trade deficits generated by other sectors.
ENGINE is a project funded by the European Union’s Horizon Europe research and innovation programme that aims to reduce the environmental impact of the manufacturing process and improve the competitiveness of metal product manufacturers by developing a novel metal product design and manufacturing system. The ENGINE system combines three integrated modules to facilitate industrial data-management, computational product and process design with in-situ diagnostics, production monitoring and control. It integrates Life Cycle Assignments in design and business decisions, reduces defects, waste, and shrinks product time-to-market.
Therefore, ENGINE will deploy, integrate, and demonstrate the first-time-right and zero-defect product design and manufacturing system with respective methodologies, and implement a supply-chain, multi-site data management solution for secure gathering, storage and sharing of proprietary industrial data. It will create a computational modelling toolbox for first-time-right manufacturing and demonstrate relevant methodologies and workflows, and develop a real-time non-destructive production monitoring solution, AI damage recognition, and demonstrate new methodologies.
Consequently, ENGINE will increase the productivity of industrial partners by enhancing their products and services with project innovations. It will also have an impact on the environment, by reducing the impact of metal product manufacturers through improved manufacturing processes, and novel repair and refurbishment strategies, and refine and integrate LCA and LCC methods into the design process to support the shift towards sustainable-by-design and circular products.
The innovations the project will produce will either follow existing standards and developed specifications or identify gaps in existing standardization and pave the way towards full standardization. The project will also develop training and upskilling materials for employees working in product design and manufacturing.
More information can be found at: https://theengineproject.eu/
This project is funded by the European Union under grant agreement No. 101058179
openZDM, a project funded by the European Union’s Horizon Europe research and innovation programme, aims to provide an open platform to support production networks’ zero-defect processes, bringing together existing R&D solutions and creating an innovative state-of-the-art integrated solution.
Through five industrial pilots in real-life operational conditions the initiative will test and finalize the technological tools and facilitate the adoption of the openZDM solution: a digital platform that builds on the state-of-the-art Reference Architecture Model for Industry 4.0 and Asset Administration Shell, non-destructive inspection (NDI) methods and data-driven quality assessment techniques for online defect identification and quality assessment. Furthermore, a Digital Twin, key enabling technology for online process adaptation and waste reduction.
The objectives of openZDM are:
- The development of non-destructive inspection systems/techniques for quality assessment (vision system, visible (VIS) range, infrared (IR) range, laser line triangulation system, x-ray diffraction)
- Digital twin for online process adaptation (a novel framework to enable zero-defect engineering and control activities in an open, collaborative multi-sided ecosystem)
- Decision making tool (evaluate alternative zero-defects manufacturing strategies, analyse “what-if” scenarios, and suggest adaptation strategies to the human or autonomously apply (self)-adaptive strategies)
- AAS enabled platform (analyse the type of data to be exchanged within a digital supply chain holistically considering the CPS, support different communication protocols, enable interoperability with the different/competing digital manufacturing ecosystem, between legacy and new systems and between proprietary and open standards by the implementation of connectors and mediators)
- Data-driven quality assessment for zero defects (extract data, store it in specialized databases and real-time stream processing and analysis at both local and global levels)
- Lifecycle assessment (assess the impact of certain zero-defect manufacturing strategies in the lifecycle of the product or the production value chain)
More information can be found at: https://www.openzdm.eu/
This project is funded by the European Union under grant agreement 101058673